
System in a Small Footprint
Precision Dental
Machining Center
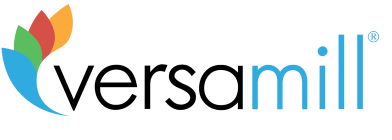
The Versamill AX-300 PRO precision dental machining center is the latest addition to our Versamill compact machine lineup. The AX-300 PRO is capable of performing not only traditional crown and bridge work, but also more complex indications using dry or wet millable materials such as hybrid abutments, partial dentures, and so on. It is designed for one-day prostheses (Lithium Disilicate, Nanocomposite) and can be easily installed in tight spaces because it is an all-in-one system.
Do not let the small footprint deceive you. The Versamill AX-300 PRO is built with the same technology as “full-frame” CNC industrial machines and is intended to perform reliably and with high precision over time.
The Versamill AX-300 PRO’s strength and rigidity, combined with the undercut machining capability of full 5-axis control, results in superior surface finishes, faster cycle times, and longer tool life while allowing you to machine virtually any material with the fewest number of bench-time millable materials.
Versamill features like heavy-duty aluminum-alloy frame,. 5kW spindle, large diameter pre-loaded ballscrews, linear guideways, zero stack tolerance rotary axes with heavy-duty gear reducers, and more enable you to quickly manufacture restorations with perfect fits and razor-sharp margins—with the minimum of profit-robbing, error-prone post-machining hand work.
8.4Ncm
class-leading TORQUE 80,000 rpm
AC SPINDLE
High-quality features not typically found in competitive products assure dependable production of restorations of superior quality for years to come.
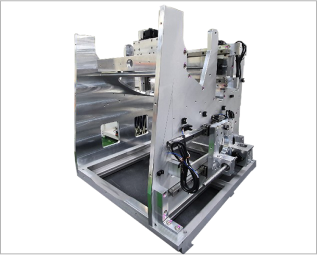
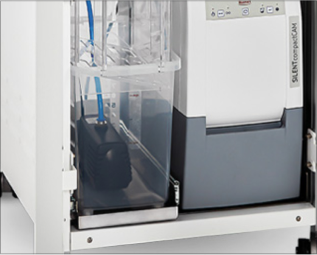
An external compressor is not required, and all additional devices (Dust Collector, Collant System) are built inside the table.
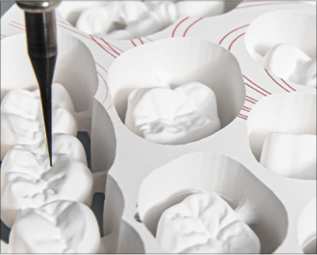
Excellent detial expression Through groove, label side texture precision processing using our 0.3mm tool for Zirconia, you can process prostheses close to natural teeth.
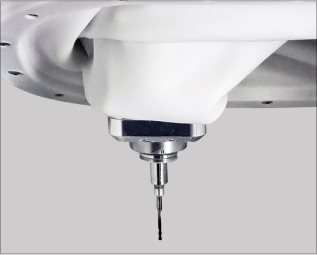
Powerful, high-speed precision spindle, class-leading, 80,000 rpm,. 5kW spindle delivers up to 8.4Ncm torque.
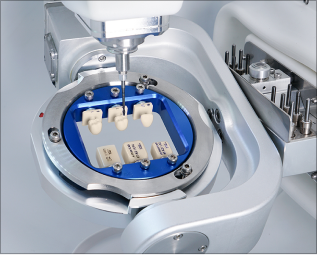

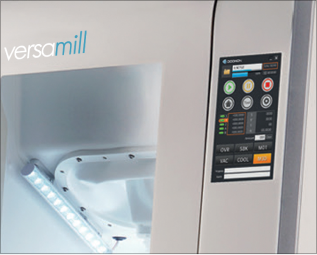
Features easy-to-use machine control developed for high-speed machining operations.
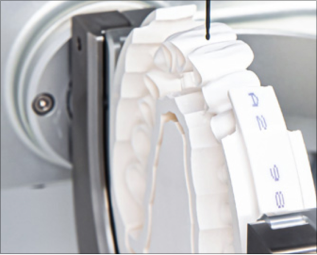
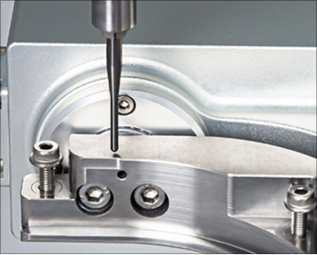
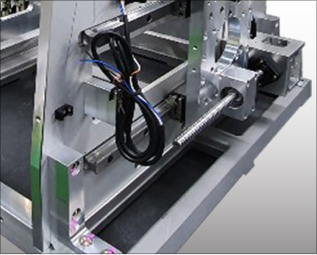
Use of precision ball screws with anti-backlash ball nuts along with linear guides and closed-loop microstepper drives assures superior dynamic motion and positional accuracy.
-
5-Axis
dental milling center
capable of 5-Axis simultaneous machining including undercuts. - Machine wide variety of materials - including: zirconia, wax, PMMA, PEEK, resins, Pekkton, nano-composits, lithium disilicate, and more.
- Ideal for the production of bridges, copings, inlays, onlays crowns, models and more.
- Long tool life and superior surface finishes due to extreme stability and minimum vibration.
- Flexible universal fixturing for quick adaption to different materials and restoration types.
- Integrated HSM machine control.
- Open architecture design compatible with industry standard software for easy integration into a complete manufacturing solution.
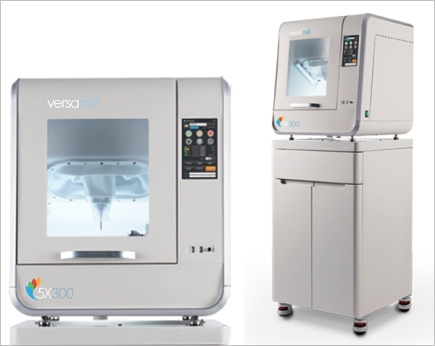
The Versamill AX-300 PRO based digital dental manufacturing system supports the manufacturing of multiple copings, crowns, bridges, inlays/onlays, hybrid abutments, dental bars, and implant bridges.
The Axsys team of experts can develop a custom open solution of hardware, software, and services to meet your unique goals and objectives. Each solution includes everything you need to achieve maximum utilization in the shortest possible timeframe.
-
Dental CAD and/or Dental CAM software.
-
Scanners.
-
3D dental printers.
-
Sintering ovens.
- On-site training & support.
- Custom fixtures.
- Consumable products.
- Raw materials & more.
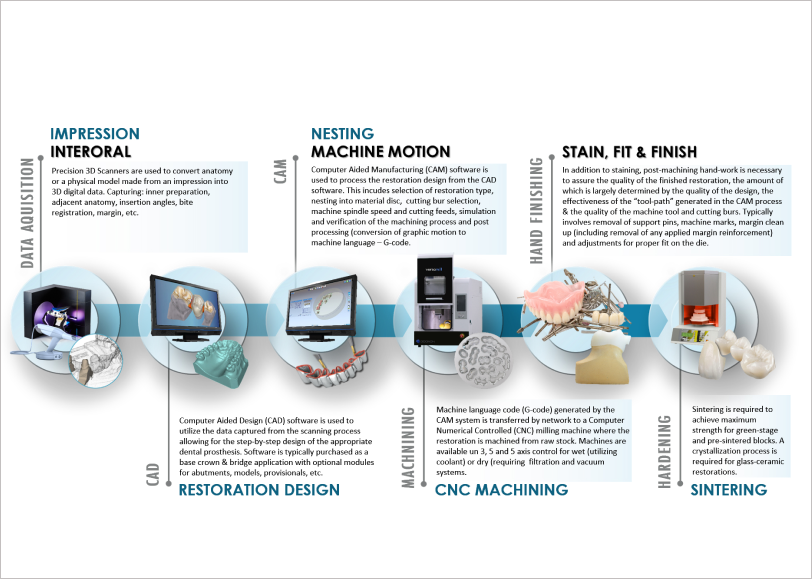
Travel Limits (X,Y & Z Axis) | 145mm X-Axis, 110mm Y-Axis, 85mm Z-Axis |
Travel Limits (A & B Axis) | ± 180 Degrees A-Axis, ± 30 Degrees B-Axis |
Maximum Feedrate (X,Y & Z Axis) | 6,000 mm/min |
Maximum Feedrate (A & B Axis) | 30 RPM |
Spindle | 60,000 RPM, .5kW Air Cooled |
Automatic Tool Changer | 12 Tools w/Tool Breakage Sensor |
Rectangular Material Block | 100mm X 100mm X 28mm |
Circular Material Block | 98.3Ø Disc |
Machine Dimensions | 540mm (W) X 580mm (L) X 630mm (H) |
Installation Space (With optional table) | 1220mm (W) X 900mm (L) X 1800mm (H) |
Optional Machine Stand Dimensions | 540mm (W) X 950mm (L) X 500 (H) |
Machine Weight | 90 kg |
Gross Weight (For shipment with optional table) | 175 kg |
Way System | Linear Guides |
Drive Mechanism | Ball Screw |
Power Supply | 120-240 VAC 50/60 Hz Single Phase, 5.5 amps |
Clamp Diameter/Tool Shank | 4.0mm |
Contrary to claims to the contrary, there are many benefits to wet-machining zirconia. These benefits extend beyond the added expense and noise associated with the required filtration and vacuum systems required for dry milling applications. These vacuum and filtration systems, while removing a large amount of the caustic zirconia dust generated by the machining process, do not remove all of the dust- the balance of which becomes air born in the lab or dental office environment and creeps into machine components thereby compromising or shortening their operational lives.
Zirconia sludge (the mixture of zirconia and water) is by far easier to deal with than dry zirconia dust, does not infiltrate machine components and is significantly less destructive to machine components than caustic and abrasive dry zirconia swarf (by-products of the machining process).
Users not only enjoy longer machine and tool life, lower operating expense, and reduced system maintenance, but also realize the benefits of highly detailed and lustrous post-sinter units, superior surface finishes and sharp margins without extensive margin reinforcement- “do-overs” due to chipped or blown out margins are very rare and if present, usually attributed to worn tooling.
We recommend washing/cleaning out the machining area, of any mill, machining any material, be done daily as part of a preventative maintenance program. It does not take very long and is not difficult to do. Flushing with a water hose works well. Use of compressed air should be done carefully with low pressure, especially with “dry” machines that do not have adequate sealing of the machining enclosure.
Do this and the machine will reward you with smooth operation and longer, care-free life.
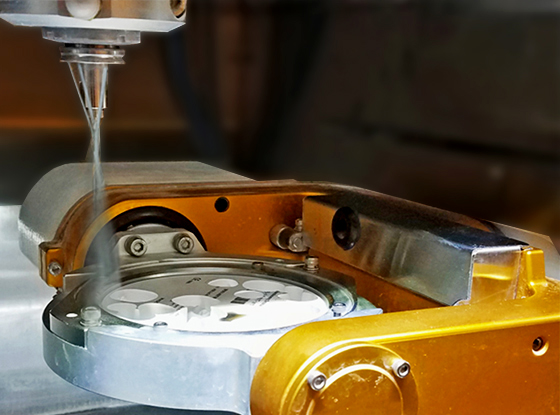
Single (70°C)): | 15 minutes+ |
Single (140°C)): | 5-10 minutes |
2-4 units (70 °C): | 40 minutes+ |
2-4 units (140°C): | 25 minutes+ |
5+ units (70°C): | 50 minutes+ |
5+ units (140°): | 25 minutes+ |
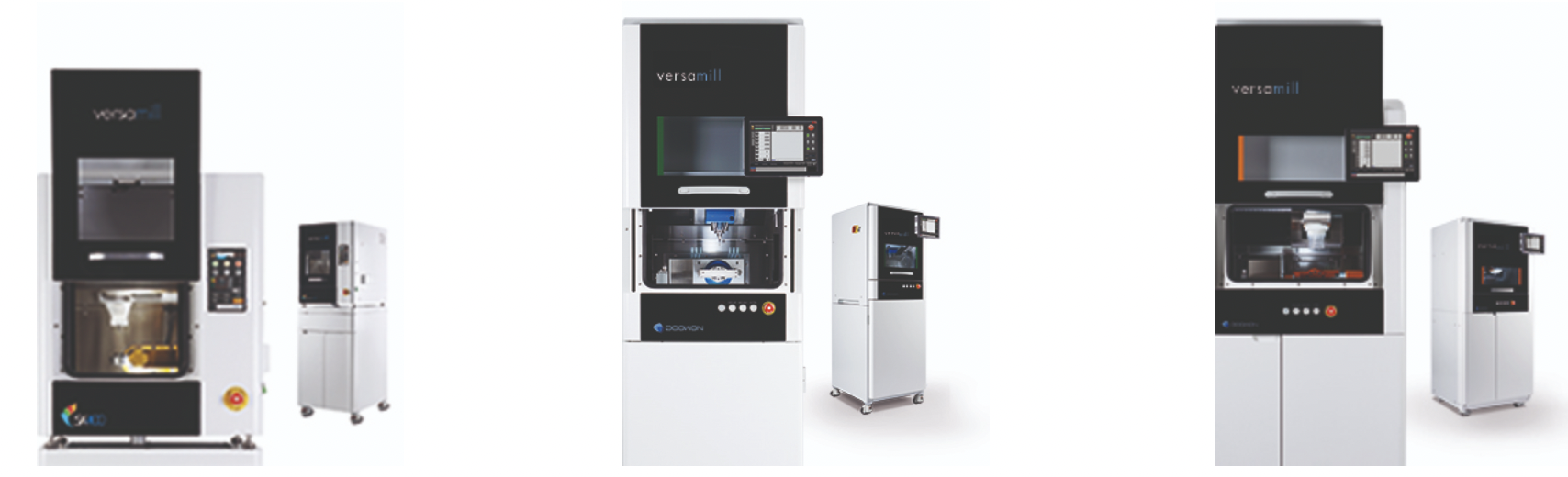
Specification | Versamill AX400 | Versamill AX-100 | Versamill AX-200 |
---|---|---|---|
Travel Limits (X, Y Z Axis) | 145 x 110 x 85 | 250 x 116 x 110 | 330 x 146 x 145 |
Travel Limits (Rotary Axis) | ±180° B-Axis, ±30° A-Axis | 360° A-axis | ±180° A-axis, ±30° B-axis |
Number of Axes | 5 Simultaneous | 4 Simultaneous | 5 Simultaneous |
Accuracy | ±10.0µm | ±5.0µm | ±5.0µm |
Repeatability | ±5.0µm | ±3.0µm | ±3.0µm |
Automatic Tool Changer | 10 Tools w/Tool Breakage Sensor | 8 Tools w/Tool Breakage Sensor | 15 Tools w/Tool Breakage Sensor |
Spindle | 80,000, 0.5kW, Air Cooled | 60,000 rpm, 1.4kW, Air Cooled | 60,000 rpm, 3.0kW, Air Cooled |
Circular Material Block | 98.3Ø Disc | 98.3Ø Disc | 98.3Ø Disc |
Machine Dimensions (W x L x H) | 545mm x 590mm x 1630mm (on 990mm table) | 623mm x 780mm x 1735mm | 745mm x 830mm x 1765mm |
Installation Space (W x L x H) | 1220mm x 900mm x 1800mm (w/ optional table) | 1100mm x 800mm x 2005mm | 1220mm x 900mm x 2025mm |
Axis Drive System | Stepper motors w/encoder, ball screws w/anti-backlash ballnuts & linear guides | Servo motors, ball screws w/anti-backlash ballnuts & linear guides | Servo motors, ball screws w/anti-backlash ballnuts & linear guides |
Weight | 100 kg (machine only) | 300 kg | 405 kg |
Gross Weight (For Shipment) | 175 kg (w/ optional table) | 365 kg | 475 kg |
Way System | Linear Guides | Linear Guides amps | Linear Guides |
Driuve Mechanism | Ball Screw | Ball Screw | Ball Screw |
Power | 120-240 VAC 50/60 Hz Single Phase, 5.5 amps | 220-240 VAC 50/60 Hz Single Phase, 15 amps | 220-240 VAC 50/60 Hz Single Phase, 15 amps |
Clamp Diameter/Tool Shank | 4.0mm | 6.0mm | 6.0mm |
Materials | Zirconia, Titanium, PMMA, Glass-ceramics, PEEK, Pekkton, Nano-composits, Resin, Wax and more | Cr-Co, Ni-Cr, Titanium, Zirconia, PMMA, Glass-ceramics, Nano-composits, PEEK, Pekkton, Wax and more | Cr-Co, Ni-Cr, Titanium, Zirconia, PMMA, Glass-ceramics, Lava Ultimate, Resin, Wax and more. |
Indications | Crowns, Copings, Bridges, Pre-mill and Hybrid Abutments & more. | Inlays and Onlays, Crowns, Copings, Bridges, Pre-mill and Hybrid Abutments & more. | Inlays and Onlays, Crowns, Copings, Bridges, Custom Abutments, Bar Overdentures & more. |
In today’s fast-paced and technology-driven world, dental practices are increasingly embracing advanced digital manufacturing solutions to enhance patient care and improve efficiency. …
Dentistry is undergoing a remarkable transformation, thanks to the rapid advancements in digital technology. From artificial intelligence (AI) and 3D printing to …
In today’s rapidly evolving dental landscape, embracing digital technologies is no longer an option – it’s a necessity. However, integrating new technologies …
The field of dentistry is undergoing a dramatic transformation, driven by rapid advancements in digital technology. From artificial intelligence (AI) and 3D …