

DEKEMA
Your Choice
DEKEMA Service GmbH based in Freilassing, was founded in 1973. The rugged design and the reliable functioning were at that time exemplary and have since then been an obligation and tradition.
The experience in development and the continuous search for the optimization of the products enabled the AUSTROMAT ceramic furnaces to find their way into laboratories all around the world.
Only DEKEMA® is able to perfectly adapt the silicon carbide heating technology to dentistry through their patent-pending technique. Sintering objects are heated without any cover. No greening or discoloration arises. This leads to a perfect temperature distribution with no shading effects and with exact temperature guidance, even with the highest heating and cooling rates.
The whole DEKEMA family of AUSTROMATs impresses with premium workmanship, a unique firing chamber concept, an absolutely intuitive user interface, and functionality that sustains any worldwide comparison.
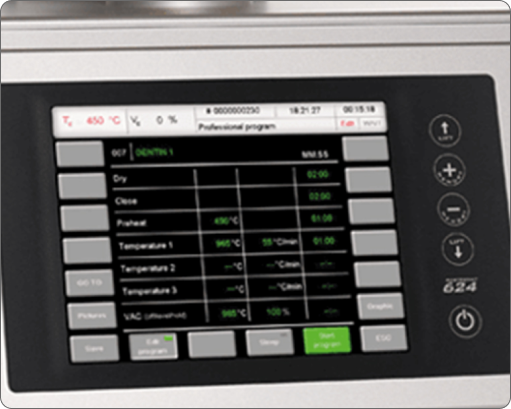
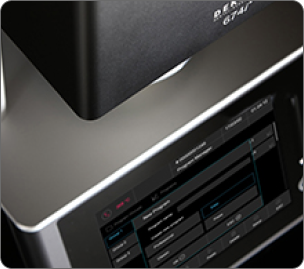
Several thousand firing, pressing, and sintering programs by nearly every manufacturer of dental ceramics are saved and maintained in this freely accessible DEKEMA data base. Load and start—as simple as that!
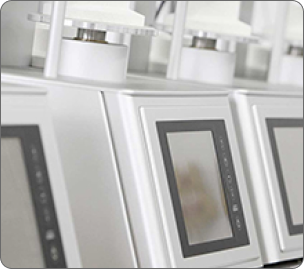
Unleash your AUSTROMAT through the unlimited possibilities of DEKEMA CONNECT. Activate the software options of your AUSTROMAT. Go online and the world of furnaces will completely change
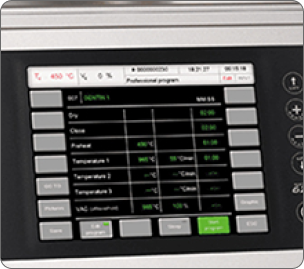
AUTODRY simulates the object temperature and automatically regulates the distance between the firing object and the firing chamber with the vibration-free lift for precise and accelerated drying, heating, and cooling phases.
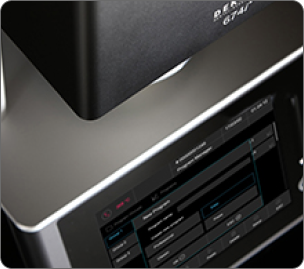
Internal test routines seamlessly monitor all relevant parameters while the program is running. An automatic diagnosis routine has also been integrated for all system components to determine the service intervals.


AUSTROMAT 624i
Ceramic furnace complete with pump, firing table,
silver wire calibration kit, tweezers and software-package.
Up to 1200°C Fire & Glaze with and without Vacuum.
Crystallize & Infiltrate with and without Vacuum.
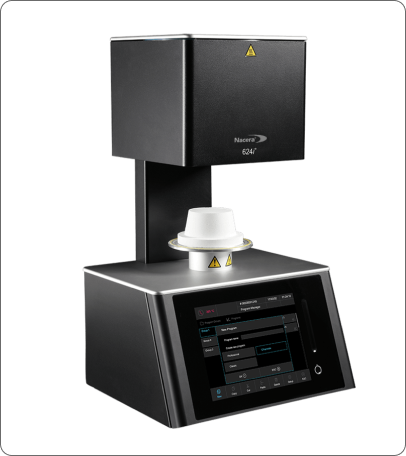
AUSTROMAT 674i
High-Temperature Sintering Furnace for temperatures up to 1560°C, Sinter, Glaze & Crystallize under Atmosphere Chairside Speed Mode
Space for all common bridge sizes or up to 40 units in one level up to Ø100mm.
Optional: Sintering in 2 levels.
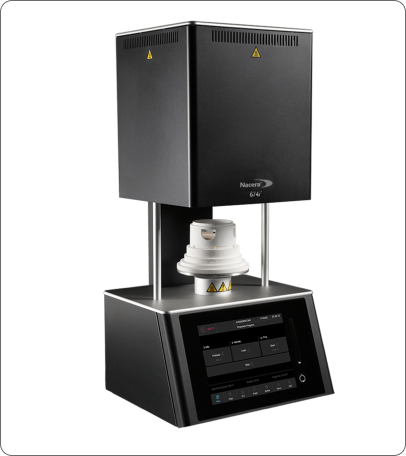

Mihm-Vogt Sintering Furnaces
Sintering Furnaces
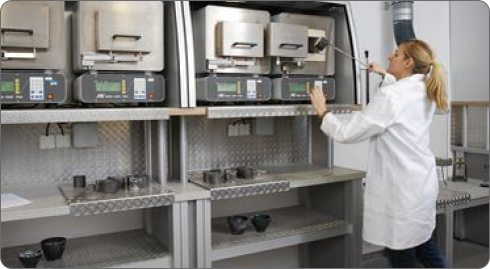
Mihm-Vogt supplies sintering furnaces for a wide range of applications and requirements: Models in widely differing versions and sizes are suitable for both small laboratories and large milling centers. They are the ideal complement to any CAD/CAM system. As a user, you can be flexible when choosing your materials without relying on one particular brand, as all our high-temperature furnaces can be programmed individually.
Mihm-Vogt speed sintering furnaces save you valuable production time and shorten the sintering process substantially, depending on the material. Speed programs use less energy and therefore help to protect the environment and reduce your consumption costs.
Mihm-Vogt only uses high-quality MoSi2 heating elements for our equipment. The highest programmable temperature is 1650 °C, but the heating elements are suitable for a temperature range reaching up to 1800 °C. Thanks to this scope in the upper temperature range, the heating elements are placed under less stress as they are not heated to their uppermost limit. This has a positive effect on their service life.
For every sintering process, there are programs of four steps available for you to use, which you can set individually. This means you can be flexible and use a variety of available sintering materials; thanks to the large temperature range, you can also use translucent zirconium oxide, for example. Choose the required end time for a process, and the furnace will start automatically.
Mihm-Vogt sintering furnaces have an emergency cooling system with off-grid housing cooling, which means that they are protected from overheating even in the event of a power cut. The ventilation continues working to ensure that, even at high sintering temperatures, your equipment is sufficiently cooled and cannot become damaged.
Our various models are adapted to your needs thanks to their sizes and equipment:
The compact and versatile HT-S sintering furnace (see figure on the left) was developed for laboratories with a limited number of restorations or laboratories with parallel milling systems. It allows you to save up to nine programs.
The HT high-temperature furnace supports you with high workloads and ideally complements your CAD-CAM system in the milling center. In addition to a large-capacity tray, this furnace also offers scope for an optional second tray. Additional functions, such as a pre-drying phase or ventilated heating, extend your application possibilities further.
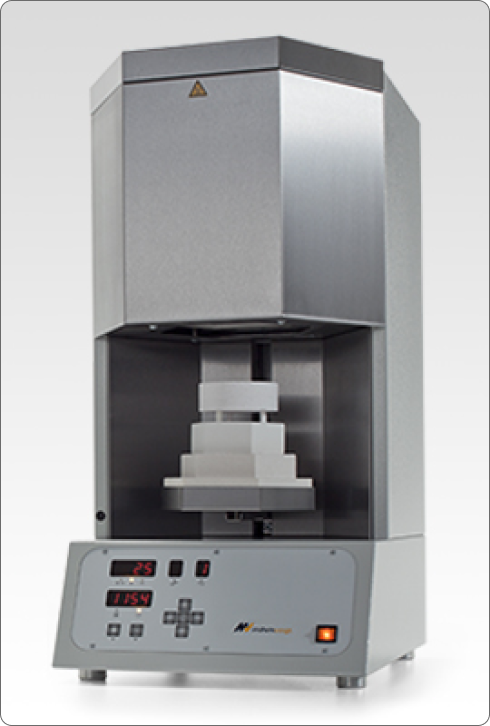
Speed Sintering
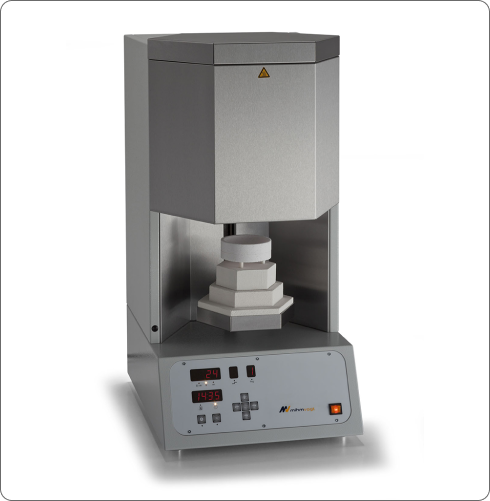
Nowadays, time and energy efficiency are decisive factors for your productivity and provide a significant advantage over the competition. Make the most of this advantage with our speed-sintering furnaces.
The market now offers zirconium oxide ceramics that withstand higher heating and cooling rates and therefore can be sintered through in shorter periods of time. For these shorter sintering processes, you need the right equipment: the HT-S Speed and HT Speed sintering furnaces (see figure on the left). Your heating system is specially developed to meet the particular requirements of speed sintering. Even the extremely long-lasting speed sintering trays are perfectly suited to this.
For you, this simply means you save huge amounts of time and have a better workload. Until now, sintering processes have been very time-consuming. However, by using suitable material, the program duration can be significantly reduced. Sintering cycles that have been shortened significantly use less energy and are therefore better for the environment, while also lowering your consumption costs.
The speed heating elements we use also offer you an additional bonus: unwanted yellow/green discoloration does not occur. Mihm-Vogt speed sintering furnaces are therefore perfectly suited to use with translucent zirconium oxide.
In addition to all of these benefits, all the functions included on our standard sintering furnaces are also available. The intelligent electronics on the Mihm-Vogt speed sintering furnaces automatically detect whether you are using a standard program or a speed program.
combine performance and ease of operation
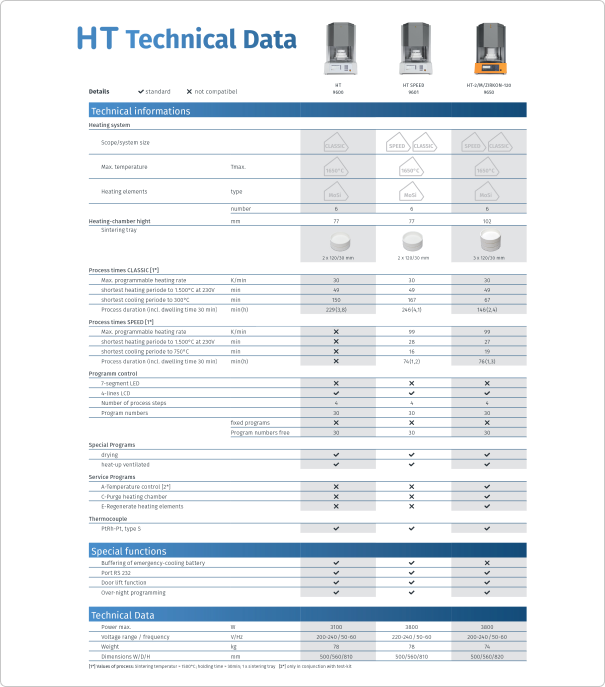
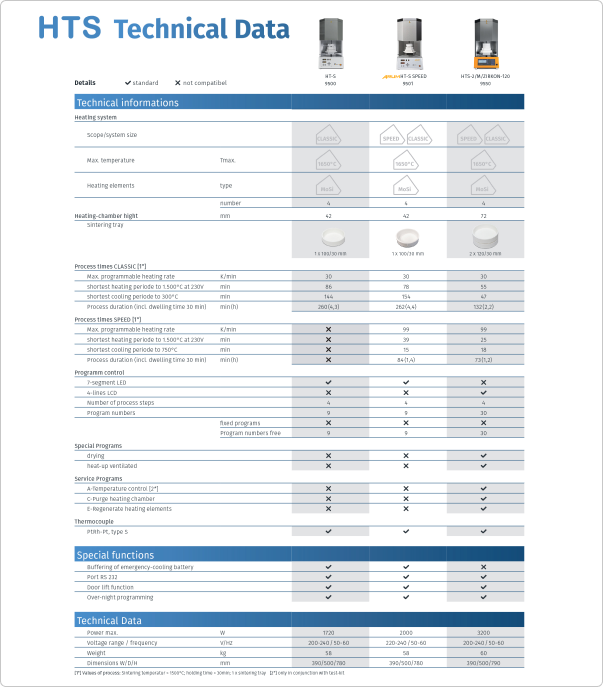
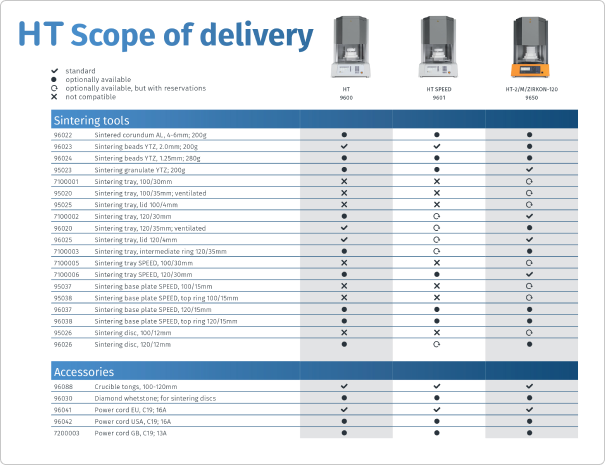
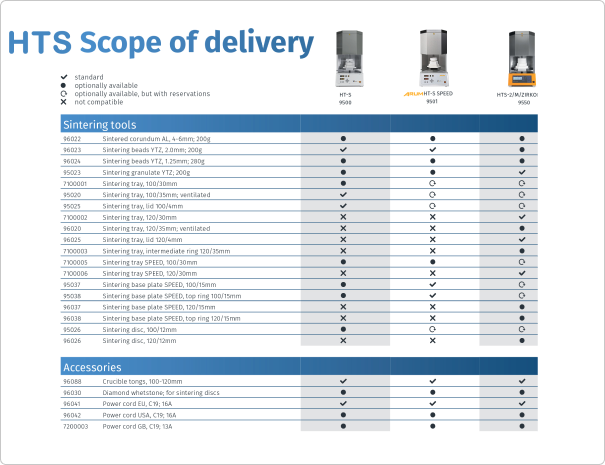